

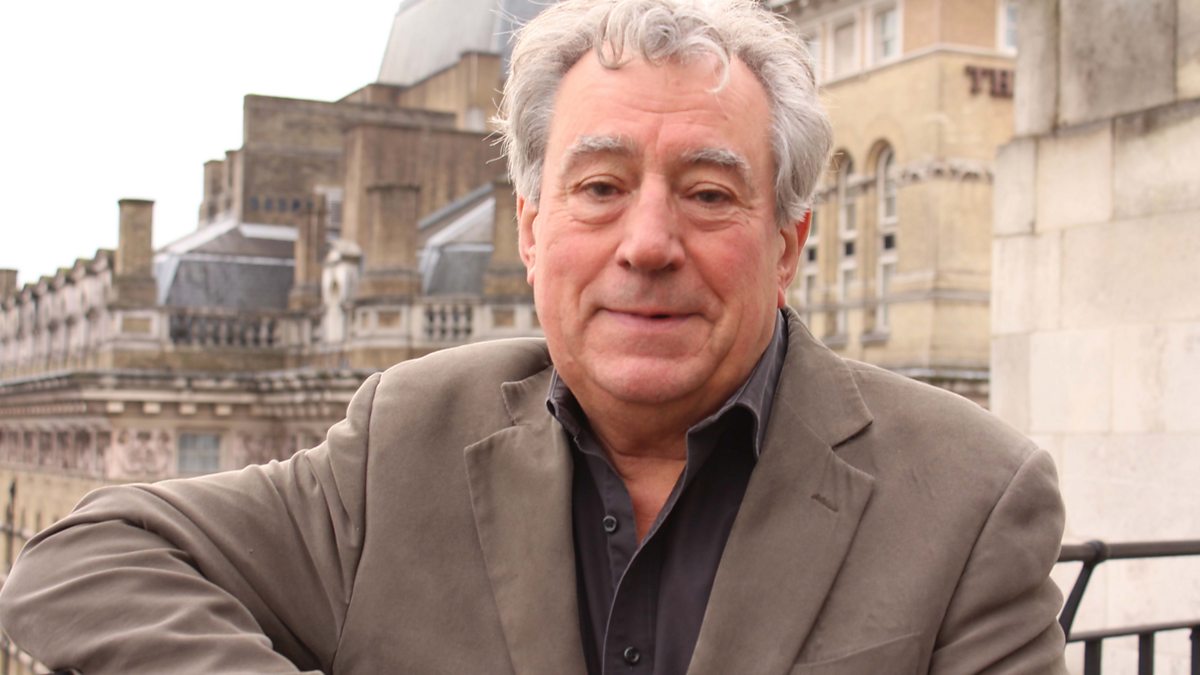
A similar trend was recognized for the oxides in EB weld line. Oxide nanoparticles in base metal were stable under present irradiation conditions as no significant change was observed with respect to the average diameter and number density. Transmission electron microscopy (TEM) and nano-indentation tests were performed after ion irradiation to investigate the post-irradiation microstructures including the stability of oxide nanoparticles and the irradiation induced hardening, respectively, with special attention paid to the comparison between base metal and EB weld line. Coupons of 12Cr–6Al-ODS steel with an electron-beam (EB) weld line were irradiated with 6.4 MeV Fe 3+ ions at 300 ☌ to nominal doses of 2.6, 7.9 and 13.0 dpa at 600 nm depth below the irradiated surface. Oxide dispersion strengthened (ODS) steels are promising accident tolerant fuel (ATF) cladding alternatives because of their excellent oxidation resistance and mechanical properties at high temperatures. Within an error range, it is possible to approximately After irradiation, the ODS alloy was found to have higher yield strength and lower ductility.įor the MDBT method, in general, the standard deviation is less than 3% for strength, but it is much larger for uniform elongation. Hence within this Summary and conclusionĪfter 1.73×10 19 n/cm 2 neutron irradiation at 290☌, the yield strength and the ultimate tensile strength of irradiated specimens increased by 5.5% and 4.2%, respectively, and the uniform elongation decreased by 12%. In comparison to the results of tensile tests, the yield and ultimate tensile strengths of the ODS alloy tested by the MDBT method are lower by 1.1% and 7.2%, respectively. It indicates that the unirradiated ODS alloy has good strength properties and modest ductility. Table 2 shows the experimental results using the MDBT method. Specimens Mechanical properties of unirradiated and irradiated ODS alloyįor unirradiated ODS alloy, the uniaxial yield strength was 848 MPa, the ultimate tensile strength was 980 MPa, and the total elongation was 17.5%.

Finally, it was annealed for 2 h at 1400☌ in vacuum and 0.35 mm thick slices were cut from annealed ODS rods, then polished to 0.3 mm thick. Original powders were mixed together by mechanical alloying (MA) under an argon atmosphere, and then thermal-extruded and rolled into rods after canistering and degassing. 1 shows the flow chart for producing this ODS alloy. The ODS alloy used in this experiment was made by a complicated technique.
